Your Total Handbook to Preventing Weld Undercut Like a Pro
Your Total Handbook to Preventing Weld Undercut Like a Pro
Blog Article
Mastering the Art of Welding: How to Prevent Undercut Welding Issues for Flawless Construction Outcomes
Performance and accuracy are paramount on the planet of welding, where even the smallest flaw can jeopardize the architectural stability of a made item. One usual difficulty that welders face is damaging, a flaw that can damage a weld joint and lead to pricey rework. By recognizing the origin creates of undercut welding and applying reliable strategies to stop it, welders can boost their craft to brand-new levels of excellence (Preventing weld undercut). In the pursuit of flawless manufacture outcomes, grasping the art of welding to prevent undercut issues is not just an ability yet a need for those aiming for perfection in their work.
Comprehending Undercut Welding
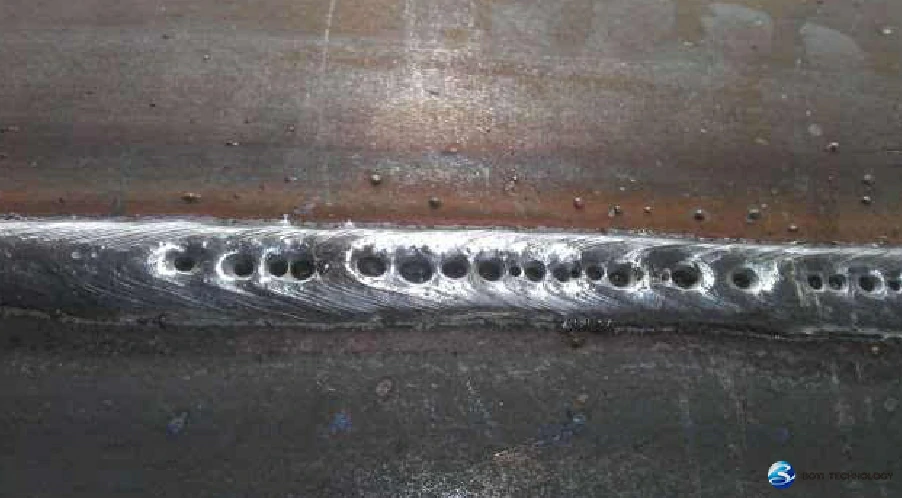
To stop undercut welding, welders need to ensure proper welding parameters, such as adjusting the current, voltage, travel speed, and maintaining the appropriate electrode angle. By recognizing the reasons of undercut welding and applying preventative actions, welders can attain high-quality, structurally audio welds.
Reasons For Undercut in Welding
Understanding the aspects that add to undercut in welding is necessary for welders to generate top quality, structurally audio welds. Poor welding inaccurate or existing welding rate can also contribute to undercut. Comprehending these reasons and applying correct welding techniques can help avoid undercutting problems, making certain solid and resilient welds.
Strategies to stop Undercutting

To reduce the danger of undercutting in welding, welders can utilize calculated welding methods focused on improving the high quality and stability of the weld joints. One efficient technique is to change the welding criteria, such as voltage, present, and travel speed, to guarantee proper warm input and deposition. Keeping an ideal electrode angle and making sure constant travel speed can also help prevent undercut. Additionally, using the correct welding technique for the specific joint configuration, such as weave or stringer grains, can add to lowering damaging. Preventing weld undercut.
Utilizing back-step welding strategies and controlling the weld grain profile can likewise aid distribute warm equally and lessen the danger of undercut. Regular assessment of the weld joint during and after welding, as well as carrying out top quality assurance procedures, can assist in finding and addressing undercutting problems immediately.
Importance of Appropriate Welding Criteria
Selecting and preserving proper welding criteria is important for accomplishing effective welds with marginal defects. Welding parameters refer to variables such as voltage, present, take a trip rate, electrode angle, and securing gas circulation price that straight impact the welding process. These learn this here now parameters should be thoroughly adjusted based on the sort of material being welded, its thickness, and the welding technique employed.
Proper welding parameters guarantee the best amount of warm is put on melt the base metals and filler material uniformly. If the parameters are set expensive, it can lead to too much warmth input, creating distortion, spatter, or burn-through. On the other hand, if the parameters are also reduced, insufficient combination, lack of penetration, or damaging might happen.
High Quality Assurance in Welding Operations
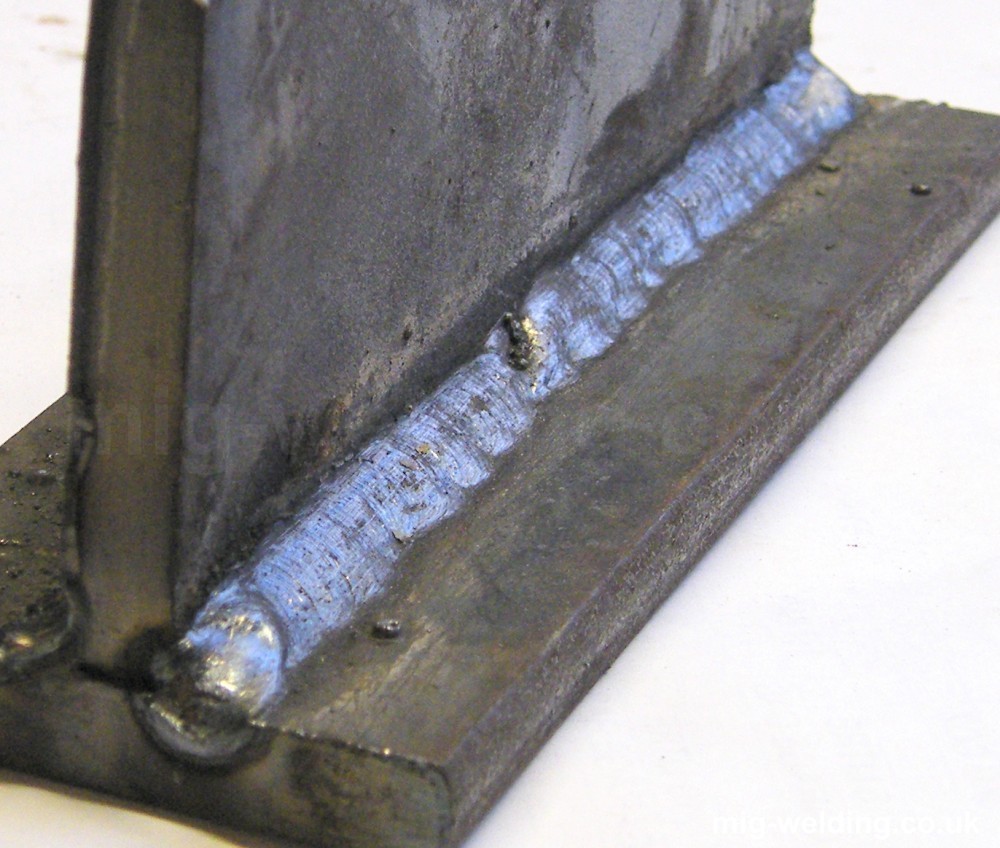
Verdict
Finally, grasping the art of welding calls for a detailed understanding of undercut welding, its causes, and techniques to stop it. By making sure proper welding parameters and carrying out quality control methods, flawless manufacture results can be attained. It is vital for welders to consistently pursue excellence in their welding image source procedures to avoid undercut problems and generate premium welds.
Undercut welding, a common flaw in welding procedures, happens when the weld steel doesn't appropriately fill the groove and leaves a groove or anxiety along the bonded joint.To avoid undercut welding, welders need to guarantee correct welding parameters, such as changing the existing, voltage, travel speed, and keeping the correct electrode angle. Insufficient welding existing or incorrect welding rate can also contribute to damage.To minimize the risk of undercutting in welding, welders can use strategic welding strategies intended at boosting the quality and stability of the weld joints.In verdict, mastering the art of welding requires an extensive understanding of undercut welding, its reasons, and strategies to prevent it.
Report this page